Как в условиях санкций в России новые шины делают
Корреспондент «СитиТрафика» под конец первого сезона эксплуатации российских шин, сменивших у нас финской бренд Nokian, воспользовался возможностью посетить шинный завод во Всеволожске и живьем увидеть, как рождается именно эта автомобильная резина.
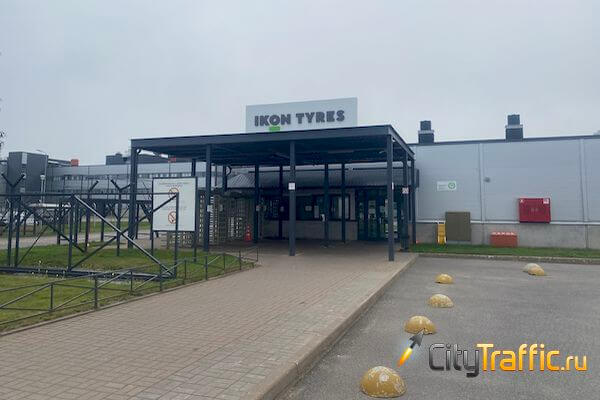
После примерно 10 тысяч километров пробега комплекта покрышек Ikon Autograph Aqua 3 на личном автомобиле довелось встретить негативные отзывы в сети. У одного комментатора произошел «разрыв боковины», у другого даже «колесо взорвалось». Собственный опыт показывает, что шины Ikon не склонны к таким фатальным неприятностям. Закрались сомнения в правдивости написанного, а лучший способ проверить – своими глазами увидеть производство данной продукции.
Наш запрос пришел на завод в Ленобласти в период активной подготовки к корпоративной игре «Что? Где? Когда?». Она была запланирована в связи с празднованием дня рождения компании. Впрочем, пресс-служба не только не отказала в посещении, наоборот, для гостя из Самарской области организовали персональную экскурсию. Показали практически каждый элемент технологической цепочки от «замешивания» сырья до проверки готовых изделий.
Предприятие, напомним, работает с 2005 года. В 2023 году был проведеён тотальный ребрендинг в связи с уходом Nokian Tyres из России. Теперь завод входит в группу Татнефть и в круглосуточном бесперебойном режиме выпускает широкий ассортимент летних и зимних шин под новым брендом.
Раз целью поездки во Всеволожск была проверка качества Ikon Tyres и знакомство с самой системой контроля шин на самом заводе, раскладывать по полочкам ассортимент продукции, изучать экономические показатели, перебирать типоразмеры, погружаться в химический состав каждого элемента мы не станем. Эти данные общедоступные. Расскажем больше про человеческое восприятие масштабного производства, посмотрим на технологический процесс глазами рядового потребителя.
Шины пока не видно
Завод может выпускать до 17 миллионов шин в год, его общая площадь 500 тысяч квадратных метров. Пока что абсолютный максимум – это выпуск 51555 шин в сутки. Он был зафиксирован в мае 2018 года. Прямо сейчас предприятие загружено не на 100%, так что потенциал для новых рекордов есть.
Экскурсию проводил сотрудник компании Игорь, работающий на предприятии без малого 15 лет. В 2010 году он начинал здесь прессовщиком-вулканизаторщиком, а нынче свои знания и богатый опыт реализует на качественно ином уровне – в проектном офисе компании.
Причина долговечности отношений с работодателем для подавляющего большинства персонала, кстати, тоже широко известна – здесь прекрасный соцпакет, есть свой спортзал и сауна, льготное питание, добротные корпоративные мероприятия и, конечно, у многих работников давно выработался еще один личный стимул – безграничная любовь к профессии.
Поверьте, ее видно в каждом жесте, в разъяснении любой малейшей операции, в глубоком знании механизмов и процессов. Похожее беззаветное погружение в свое дело и знание любых нюансов, а еще радушный и профессиональный прием прежде приходилось наблюдать, например, на АВТОВАЗе и в стенах компании «LADA Sport», где люди, влюбленные в свою работу, создают гоночные автомобили LADA. Впрочем, мы слегка отвлеклись от содержательного рассказа о процессе изготовления автомобильных шин.
Вкалывают роботы
Первое, на что сразу обращаешь внимание, – автоматика. Повсюду автономные погрузчики AGV, способные непрерывно до 8 часов на одной зарядке туда-сюда возить разные грузы, а затем самостоятельно возвращаться на станцию для подзарядки аккумуляторов. Вверху под потолком производственных помещений перемещаются другие вертикальные и горизонтальные транспортировщики всего подряд – от резиновой смеси до заготовок и готовых шин. Различные роботизированные «руки» с хирургической точностью выполняют предписанные им задачи. Даже пресс вулканизации обеспечивается автономной установкой – операторы тут нужны лишь для периодической замены пресс-формы, общего контроля и других операций.
Интересно и то, что самоходные тележки не только перевозят сырье – они еще осуществляют съем сырья с линий по их производству, самостоятельно загружают и разгружают его со стеллажей для хранения. Даже на складе готовой продукции шины принимает… робот. Это огромный колосс, посмотреть на который не удалось, так как на склад и в цех, где происходит установка шипов в зимние шины, посторонних не водят. Впрочем, экскурсия и без того заняла более двух часов.
В том числе и в силу существенной автоматизации процессов и из-за огромного количества специфических терминов и наименований не беремся точно воспроизвести все, что увлекательно рассказывал наш экскурсовод, но общим представлением поделимся.
Контроль всего подряд
Современная шина, которую видит водитель, состоит из нескольких компонентов. Для ее создания на предприятии полного цикла от сырья до готовых покрышек, а Ikon Tyres именно такой завод, сначала изготавливают базовую смесь. В ее составе резина, сажа, силика и прочие химические элементы, каждый из которых в дальнейшем будет отвечать за такие характеристики шин, как эластичность, сцепление с дорогой и т. д. Раскрывать рецептуру, понятное дело, не принято, это сродни семейным кулинарным секретам.
Первоначальная смесь совершенно не выглядит пригодной для изготовления покрышек. Она скорее внешне напоминает вспененный резиновый коврик. Но после нескольких циклов смешивания текстура становится однородной, к ней добавляются в зависимости от требуемых параметров готового изделия разные природные и синтетические каучуки и иные компоненты, то, что получается на выходе, называют финальной смесью.
Отдельные элементы будущих шин, например, протектор, боковину и гермослой изготавливают на «длинных» производственных линиях. Гермослой - это один из компонентов шины, который позволяет использовать шину без камеры, именно он запирает воздух внутри и совместно с другими элементами шины не позволяет ему выйти наружу. Процесс здесь трудоемкий. А за выпуск бортового кольца (оно, кстати, может содержать от 13 до 44 витков стальной проволоки в зависимости от размера и требуемых характеристик шины) отвечает одна из «коротких» линий.
Второе, что трудно не заметить внутри производственного процесса Ikon Tyres, – строжайший контроль качества всего и вся. Даже на первых ступенях рождения автомобильных покрышек. Проверяются сырье, первичная, а затем финальная смесь, потом тестируется каждый компонент до момента сборки шины. Такая щепетильность в работе и безусловное внимание даже к самым мелким деталям внушают уважение. Тут не то что партию брака, даже отдельную «кривую» покрышку никто на склад не выпустит.
Не тонко, вот и не рвется
На наших глазах массивный экструдер смешивает сразу четыре разных резиновых смеси для премиальной шины Ikon Autograph Ice 9 – той самой, что позволила установить минувшей зимой несколько рекордов на фестивале автоспорта «Дни скорости на льду Байкала – 2024». Чтобы ни человек, ни другие машины впоследствии не перепутали, что и куда предназначено, функционирует четкая система идентификации. Каждая мелочь имеет свой номер, с ним сохраняются и детальные параметры происхождения – состав, рабочая смена и т. д. Представьте, на каждой телеге есть устройство, в которое занесены идентификационные данные того, что на нее сложили.
Далее идем к станкам, которые изготавливают нейлоновый бандаж и текстильный корд. Это, соответственно, прочные нити, формирующие «скелет» шины. До момента сборки они дополнительно прорезиниваются и совместно с гермослоем, который находится на внутренней части шины, впоследствии надежно «запирают» воздух внутри шины, придают ей прочность. Благодаря данному продольному и поперечному «каркасу» обеспечивается и устойчивость к боковым ударам, порезам, проколам и грыжам. Эти элементы отражены на готовой шине в виде индекса скорости (нейлоновый бандаж) и индекса нагрузки (корд).
К слову, бандаж укладывают вдоль оси вращения шины, а корд наносят перпендикулярно. Потому-то в информации о любой современной покрышке фигурирует латинская буква R, то есть, «радиальная». А ведь многие считают, что это радиус колеса в дюймах. Еще в состав шины добавляется стальной брекер – слой проволоки, нитки которой аккуратно подогнаны друг к другу под углом относительно вращения шины. Они расположены сразу под протектором в два слоя с противоположным направлением нитей и защищают шину от порезов, а также придают жесткость шине в районе протектора для увеличения пятна контакта с дорожным покрытием.
Следующая остановка – у внушительных размеров агрегата, который наматывает из стальной проволоки бортовое кольцо. Это жесткий обод по внутренней стороне покрышки, который будет прилегать к колесному диску. Потом с ним и резиновой смесью уже другой робот собирает бортовое крыло – крайне жёсткое плотное резиновое соединение бортового кольца с будущей боковиной.
Промежуточный итог подводит еще одна громоздкая, но высокоавтоматизированная машина, собирающая заготовку шин – она соединяет вместе все элементы, которые мы перечислили выше. На выходе получается болванка, отдаленно напоминающая шину. Теперь все предварительные процедуры позади.
15 минут - и готова новая шина
Заготовку доставляют в пресс, внутри которого специальная резиновая диафрагма раздувается, придавая будущей шине нужный объем и фиксируя ее в одном положении в момент закрытия пресса. Затем пресс с матрицами проектора и бокового рисунка запирает все вместе примерно на 15 минут при нужной температуре для процесса вулканизации, заодно придавая нужную форму готовому продукту.
Между прочим, именно здесь самостоятельно производят не только резиновую диафрагму, ресурс которой рассчитан примерно на 300-400 шин, но и пресс-формы, что обеспечивает автономность работы без сбоев и лишних перерывов. То есть производитель шин изначально меньше зависит от поставщиков оснастки.
Готовая шина после пресса некоторое время отдыхает, ведь ее ждет следующий этап контроля качества. Сначала каждое изделие внимательно осматривает человек и ставит свой именной штамп, отправляя шину на комплекс автоматических испытаний. Если же покрышка не прошла контроль (такое бывает крайне редко, но все же, прим. авт.), ее дальнейшая судьба определена однозначно – в утилизацию! Боковину тут же разрезают, что полностью исключает ее какую-либо дальнейшую эксплуатацию. Перерабатывает брак не сам шинный завод, а сторонний подрядчик. Резину, как правило, применяют в качестве сырья для автомобильных брызговиков, ковриков и других резиновых изделий, не требующих точности в качестве инертного наполнителя, или же нарезают в крошку для применения в производстве травмобезопасных покрытий.
Автоматическая проверка тут тоже отличается крайней придирчивостью. Шины среди прочих контрольных тестов впервые проходят балансировку. Каждый параметр скрупулезно заносится в базу данных и сохраняется там длительное время. В случае с зимними шинами заключительным этапом является установка шипов. Не вклейка, а именно механическая посадка каждого шипа в отведенное ему отверстие, повторяющее форму шипа.
Финал – это склад готовой продукции. Он может вместить 1,7 млн шин. При этом 550 тысяч из них способен хранить полностью автоматизированный складской комплекс. Да, часть шин из каждой партии отправляют не на склад, а… на контроль соответствия заявленным параметрам, но уже на испытательном полигоне и в лаборатории.
Коротко про маркетинг, гарантию и впечатления
Подводя итоги, мы поинтересовались разбивкой производственного плана завода. Увидели в основном производство зимних шин, ведь на дворе осень. Когда же будут производить летние шины? Выяснилось, что резину впрок не делают – весь техпроцесс напрямую связан с поступающими заказами. Практика такова, что в марте завод приступает к сборке летнего ассортимента, а уже в июне приходят первые запросы на зимнюю линейку.
Напомним, что финская расширенная гарантия Nokian была, пожалуй, лучшей в РФ. Прокол, порез, разрыв или грыжу обычно даже не осматривали – просто выдавали покупателю взамен новую шину. Только продукцию этого бренда можно было купить в любом количестве – хоть по одной шине каждого размера. На данный момент прослеживается преемственность – Ikon Tyres гарантирует ремонт лишь при проколе по центральной части протектора с диаметром отверстия не более 6 мм. Все остальное – под замену. Собственно, посетив производство, не удивляешься, почему производитель предоставляет пожизненную гарантию на свою продукцию.
Заканчиваем тем, с чего начинали. Редким авторам жалоб, наверное, стоит напомнить о простых правилах, которые почти всегда упорно игнорирует подавляющее большинство беспечных российских водителей. Шиномонтаж лучше производить в цивилизованных мастерских, а не в вагончиках. На колесных дисках экономить не надо – новый комплект резины взамен зажеванных шин выйдет дороже. А еще надо периодически обращать внимание на давление в шинах: разрыв боковины происходит лишь при продолжительной езде на спущенном колесе. Это можно утверждать со всей ответственностью. Ну, и переобувать автомобиль лучше вовремя, а не когда придется.
Под впечатлением от увиденного технологического процесса впору присматривать себе на зиму что-то из продукции этого бренда. Во-первых, сами заводчане говорят, что качеством своих шипованных шин довольны, поскольку оно – на уровне мировых стандартов. Во-вторых, на парковке у завода почти все машины были обуты в то, что производят тут же – во Всеволожске.
Андрей Серегин, фото автора
может заинтересовать
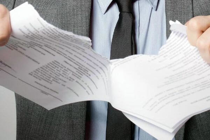
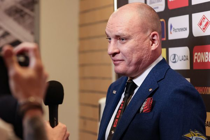
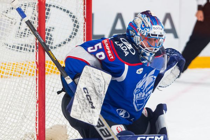
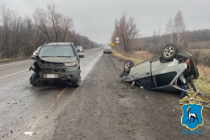
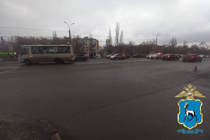
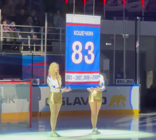
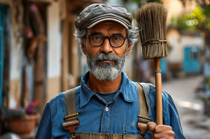
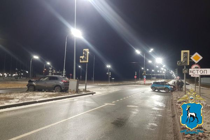
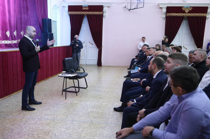
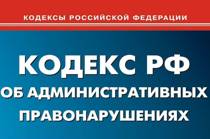
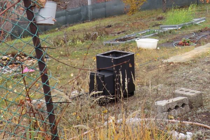
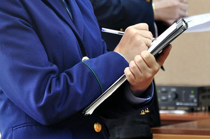